Reducing Fugitive Emissions with Stainless Steel Valves
Fugitive emissions can be a problem for any industry, but they are especially problematic in the petrochemical and refining industries. The leaking gas from these industries is composed of many different hydrocarbons such as equipment leaks and gas from the manufacturing process that have been found to cause respiratory problems, heart disease, cancer and other illnesses.
What are the Fugitive Emissions?
This type of emission is the release of chemicals into the air from unintended sources. These releases can be accidental or deliberate, but they are not always intentional. They sometimes come from leaks in storage tanks, machinery malfunctions, and unintentional venting during normal operations.
This has been an issue faced by many manufacturers because it’s costly and detrimental to the environment. They account for about 3% of all man-made global warming since 1850 by releasing methane into the atmosphere. Methane is a particularly potent greenhouse gas, with global warming potential (GWP) more than 25 times that of carbon dioxide over a 100-year period. This makes controlling fugitive emissions a crucial environmental responsibility for industries handling volatile organic compounds (VOCs) and hydrocarbons
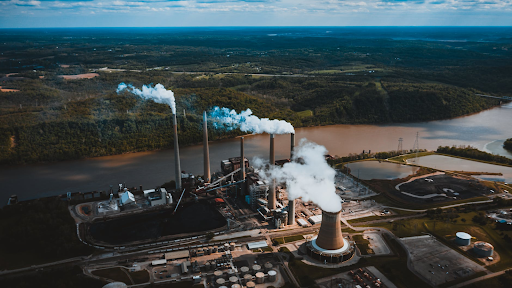
How to Mitigate this Issue?
KDV is looking to reduce emissions by promoting the use of diaphragm valves in place of other types of valves where appropriate. Most people don’t think about valves much. They just turn them on and off when they need to, but do you know how many different types of valves exist? One of the oldest is the Stainless Steel Diaphragm Valve, it’s available on the market and addresses this issue by nature of its design. Diaphragm valves are particularly useful in applications that demand high purity, corrosion resistance, and minimal maintenance, such as pharmaceutical, chemical, and food processing industries.

The reason is that the design of these diaphragm valves means that no packing or body gaskets are required. The material compatibility is also an advantage because it can be used with many different types of fluids, gases and solids without corrosion occurring on the metal parts. All bonnet components are isolated from the media by the diaphragm forming a hermetically sealed envelope with the valve body, thus eliminating the common leak path found in the other valves types. This means that stainless steel diaphragm valves are especially beneficial in applications where preventing fugitive emissions is a priority, such as in oil and gas refineries and chemical plants.
It’s important to know that there are many ways you can reduce fugitive emissions. Most of the time, when people think about reducing emissions they focus on the plant or facility where the air is emitted. This is not always the best way to go because if you’re in a different state, it may be impossible for your plant to comply with regulations in other states. The best way to reduce fugitives is by stopping them before they escape into the atmosphere. Check for leaky valves, leaks from pipe connections or joints, faulty seals around doors and windows. Regular maintenance and inspections of valve systems, along with the implementation of emission monitoring programs, can help in early detection and mitigation of leaks.
The last thing you want is an emission problem at your plant and then find out it’s too late because all of the pollutions have already escaped into our environment! This is why compliance with fugitive emission testing standards, such as ISO 15848-1 or API 624, is essential for ensuring that valves perform effectively in preventing leaks. Check valves, in particular, should also undergo these tests, as they are commonly used in systems requiring tight shut-off to prevent backflow and unintended emissions.
The effects of fugitive emissions on the environment are significant, but there is a way for manufacturers and other entities to reduce this problem. For this reason, it’s important to consider using stainless steel instead of other materials because they don’t emit any hydrogen chloride gas during their normal operation cycle which can be harmful to both workers and the environment around them. Furthermore, stainless steel valves are resistant to corrosion, which enhances their longevity and reliability in industrial applications, reducing the likelihood of leaks developing over time.
FAQS for Stainless Steel Valves
-
What are the key advantages of using stainless steel valves in high-temperature and high-pressure applications?
Stainless steel valves offer excellent mechanical strength, oxidation resistance, and thermal stability, making them ideal for extreme operating conditions. Their ability to withstand high-pressure environments and temperature fluctuations without deformation or corrosion ensures long-term reliability in industries such as oil and gas, chemical processing, and power generation. -
How do stainless steel valves compare to other materials in terms of corrosion resistance and lifecycle cost?
Stainless steel valves, particularly those made from grades such as 316 and duplex stainless steel, provide superior resistance to corrosive media, including acids, seawater, and harsh chemicals. While their initial cost is higher than carbon steel or brass valves, their longer lifespan and lower maintenance requirements reduce overall lifecycle costs, making them a cost-effective choice for critical applications. -
Can stainless steel valves be used in sanitary or pharmaceutical applications, and how do they meet hygiene standards?
Yes, stainless steel valves, especially those with a polished finish and FDA-compliant elastomers, are widely used in food, beverage, and pharmaceutical industries. Diaphragm valves, ball valves, and butterfly valves designed for sanitary applications have smooth, crevice-free surfaces to prevent bacterial growth and ensure compliance with industry standards such as ASME BPE and EHEDG. -
What factors should be considered when selecting the right stainless steel valve for an automated process control system?
Key considerations include the type of media, pressure and temperature ratings, flow control requirements, and actuation method (pneumatic, electric, or hydraulic). Additionally, compatibility with existing control systems, response time, and maintenance accessibility play a crucial role in ensuring optimal performance and reliability in automated operations. -
How do storage and handling practices impact the performance of stainless steel valves, particularly when stored alongside carbon steel?
Improper storage of stainless steel valves near carbon steel components can lead to cross-contamination and surface contamination with iron particles, resulting in corrosion (known as “rust contamination” or “tea staining”). To prevent this, stainless steel valves should be stored separately in clean, dry environments and protected with non-reactive coverings to maintain their corrosion resistance and surface integrity. -
How do stainless steel valves compare to other materials in terms of corrosion resistance and longevity in aggressive media applications? Stainless steel valves, particularly those made from 316, duplex, and super duplex grades, offer superior resistance to corrosion from acidic, saline, and chemically aggressive environments compared to carbon steel, brass, or cast iron. Their high chromium and molybdenum content forms a passive oxide layer that prevents oxidation and pitting. This ensures a longer service life in applications such as chemical processing, marine environments, and high-purity industries.
-
What are the key considerations when selecting a stainless steel valve for high-pressure and high-temperature applications? Key factors include material grade (e.g., 316 for corrosion resistance or 304 for general use), pressure rating (ANSI or DIN standards), temperature tolerance, and sealing materials (PTFE, graphite, or metal seats). For extreme conditions, reinforced stainless steel alloys like 17-4 PH or Inconel-clad components may be required. Proper selection ensures durability under thermal cycling, pressure fluctuations, and mechanical stress.
-
How does the surface finish of stainless steel valves impact their performance in sanitary and pharmaceutical applications? A smooth, polished surface (electropolished or mechanically polished to Ra ≤ 0.4 µm) prevents microbial buildup and product contamination, ensuring compliance with sanitary standards like ASME BPE, FDA, and EHEDG. Rough surfaces can trap particles and foster bacterial growth, reducing hygiene levels in biopharmaceutical and food industries. The right finish enhances cleanability and process integrity.
-
What are the best practices for maintaining and extending the service life of stainless steel valves in automated process systems? Regular inspection for wear, corrosion, and seal degradation is essential. Implementing a preventive maintenance schedule, ensuring proper lubrication of moving parts, and protecting valves from temperature or pressure shocks can significantly extend service life. Using compatible cleaning agents and avoiding chlorides (which can cause pitting) helps maintain corrosion resistance. Automation components, such as actuators and sensors, should also be regularly calibrated and tested for optimal operation.
-
Are there specific fugitive emission standards that stainless steel valves must comply with, and how do they perform in leak testing compared to other valve types? Yes, stainless steel valves used in industrial applications must meet fugitive emission standards such as ISO 15848-1, API 624, and EPA Method 21. These standards define permissible leakage rates and test procedures. Stainless steel valves, especially those with metal bellows or diaphragm seals, perform exceptionally well in leak prevention due to their durable construction and ability to maintain tight shutoff. Compared to standard packed valves, stainless steel diaphragm and bellows-sealed valves eliminate common leakage paths, ensuring superior emission control in critical applications.
KDV Flow manufactures and holds large stock of Lined Valves and other diaphragm valve types available at our office at 55 Westland Square, Beeston, Leeds LS11 5SS, United Kingdom
If you need help finding high-quality products or need any assistance designing an effective flow system contact KDV Flow today!